Metal roofing: Standing seam versus screw-down systems
Top-quality roofing is critical to keeping the contents of your structure safe, comfortable and dry. Learn about the types of metal roofing systems in our ongoing series about the components used in steel building construction.
When considering ideal roof design for your pre-engineered metal building project, two primary systems dominate the market: standing seam and screw-down panels. Understanding the differences between these options can help you make an informed decision that balances cost, durability and aesthetic appeal.
Summit Steel Buildings offers customized building solutions to suit your business goals. We can provide either system explained within this article and are only limited by your structural needs and design choices. Speak with our leadership team to decide the best system for you and we’ll provide a free quote and
preliminary drawings.
Standing seam roofing: Premium protection
Standing seam metal roofing consists of panels that lock together at the seams using a hidden fastener system. Clips beneath the raised ribs secure the panels while allowing them to expand and contract freely as temperatures change. The finished look is cleaner and more elegant because fasteners cannot be seen from the outside.
"Standing seam roofs offer longer lifespans and less maintenance compared to screw-down roofs," according to Darren Sperling of Summit Steel Buildings. This premium system can last 50+ years with minimal maintenance, making it potentially the last roof you'll ever need to install.
The hidden fastener design eliminates penetrations through the metal panels, significantly reducing the risk of leaks. Additionally, the clean, modern appearance of standing seam roofing enhances curb appeal and is particularly well-suited for premium metal options like copper, stainless steel and zinc.
Maintenance requirements are minimal, limited primarily to clearing debris and occasional cleaning.
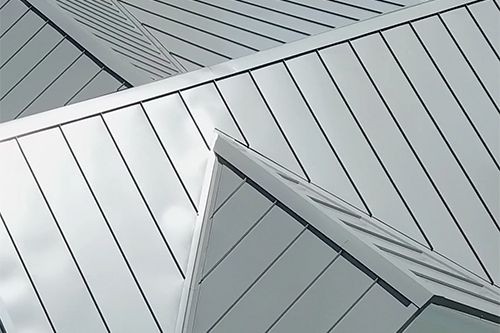
Screw-down roofing: Budget-friendly option
Screw-down roofing (also called exposed fastener) features panels secured directly to the roof deck with screws and washers visible on the panel surface. This straightforward system is more affordable and much quicker to install. The easier installation translates directly to lower pricing.
However, the direct attachment method prevents panels from moving freely during thermal expansion and contraction. Over time, this movement can cause the screw holes to enlarge, backing out fasteners and potentially creating entry points for water.
"A screw down metal roof should last 20 to 30 years depending on maintenance," Darren notes. “The screws shouldn’t rust as they’re either long life or stainless steel and are painted with the same finish as the panels.” Regular maintenance primarily involves to periodic checks around roof penetrations and potentially replacing some of the screws before leaks develop or storm damage occurs.
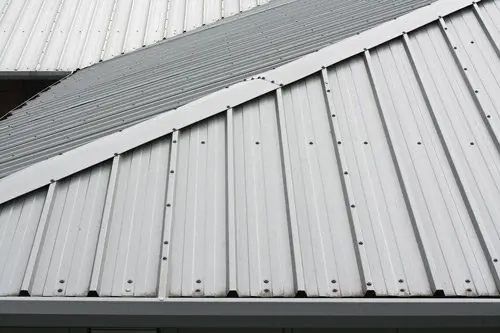
Making your best roofing choice
The decision between these systems often comes down to factors as budget considerations and aesthetic preferences. Screw-down systems offer immediate cost savings, making them popular for agricultural buildings and warehouses where construction costs are paramount. On the other hand, standing seam provides a cleaner, more sophisticated appearance without visible fasteners and are much easier to maintain.
Occasionally, the chosen system of roofing used can be dependant on roof shape, slope or design in rare architectural cases. In most cases, a standing seam metal roof is preferable over heated spaces or working and production areas where thermal movement is significant. While more expensive initially, standing seam roofing's longer lifespan and reduced maintenance needs make it more economical over time.
Roofing systems tailor made for each particular business use
Every pre-engineered metal building is designed to suit a client’s individual needs and budget. Each form of roofing engineering will provide advantages to different types of uses – the industrial storage building for raw materials is drastically different from a golf course and country club event space, for instance. Summit Steel Buildings recommends standing seam roofing for most applications: "It provides a nicer finished look and resists leaking much better since no holes are actually punched into the roofing panels."
However, both systems have their place. For budget-conscious projects with shorter-term expectations, screw-down roofing remains a practical solution. For premium applications where longevity, weather resistance and appearances are priorities, standing seam represents the superior investment.
Whichever system you choose, proper installation by the qualified professionals at Summit Steel Buildings remains critical to achieving the full performance potential of your metal roofing system.
Contact our experienced pre-engineered building solution team
online, by
email or by calling us at
1-877-417-8335 to obtain a free quote and preliminary drawings.
Read the other articles in our "Know your steel components" series:
Pre-engineered steel panels
- More than a pretty face
- Benefits of building with pre-engineered steel panels
- Steel panel and colour design
- Be inspired by colour
Girts
Purlins
Concrete foundations
Roofing
Windows
About the author
Darren Sperling has specialized in the engineering and delivery of pre-engineered steel buildings for over 20 years and
has experience in over 20 countries worldwide. He can be contacted at Summit Steel Buildings at (877) 417-8335, by email at
darren.sperling@summitsteelbuildings.com or on
LinkedIn.