Considerations for adding an ideal warehouse
Store more in the ideal environment of a pre-engineered steel building.
In a growing Canadian economy, industrial and commercial enterprises are required to invest and expand their production and logistics capacity. Logistics and warehousing are two of the most important factors in capacity and supply chain management to prevent bottlenecks, disorganization and delays. Although both terms are commonly used within the shipping industry, they mean different things. Warehousing refers to the storage of goods. Logistics involves warehousing along with several other functions in the movement of goods from one place to another. In both uses, the need for a well-designed building to operate supply and inventories is essential.
Warehouse space is a valuable investment because of the future revenue it creates and real estate value (both size and location). The benefit of building new is that you get the exact structure you need and don’t have to worry about retrofitting or dealing with old structural damage.
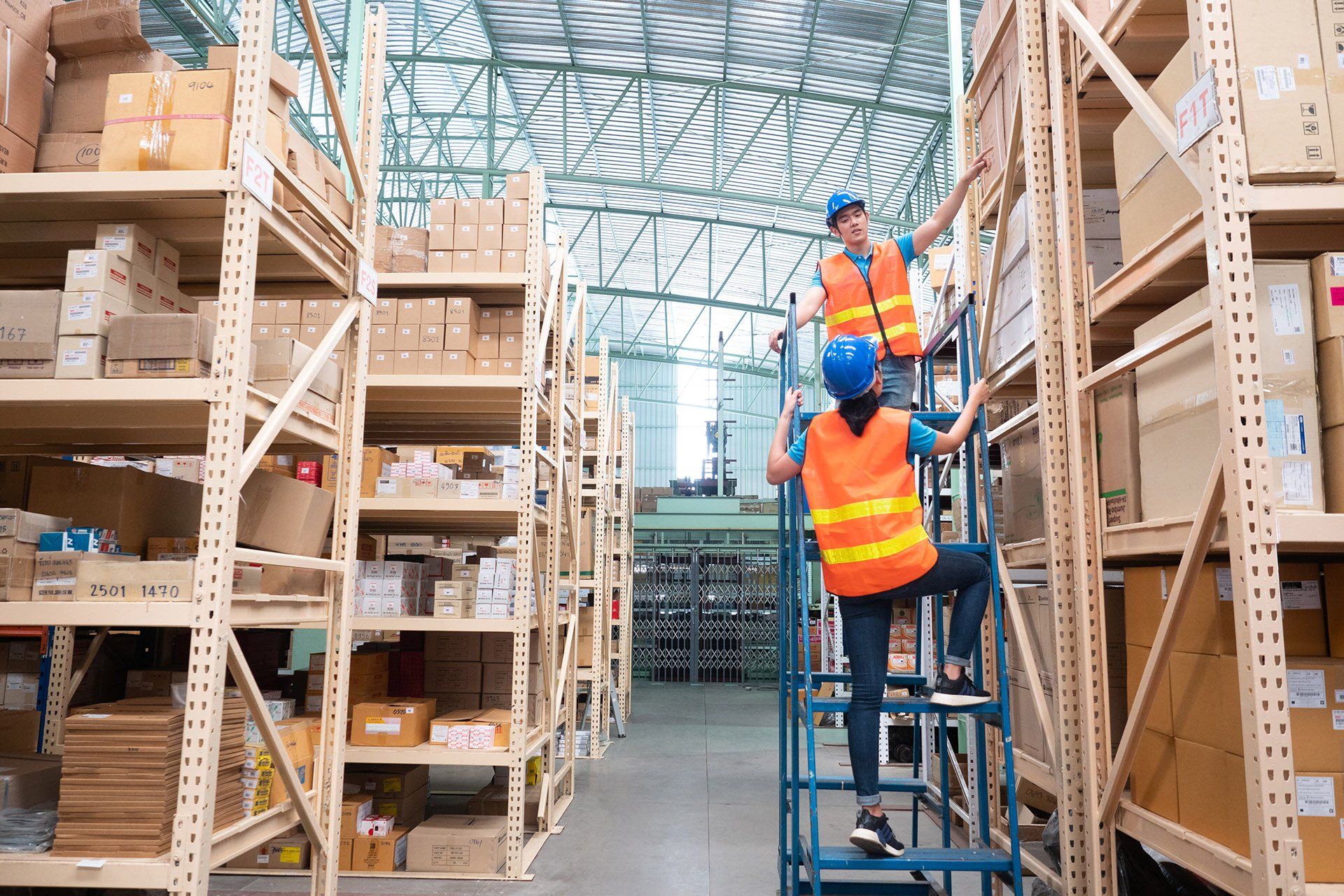
For construction purposes, warehousing building types fall into two basic types by application:
1. General warehousing and storage
Probably what most people consider as traditional commercial storage buildings, “dry warehouses” are used for storing products, expanding retail channels, or as a co-packing facility or fulfillment warehouse. E-commerce has created a huge opportunity for both short- or long-term pick-and-pack storage (sometimes know as 3PL – third-party logistics service solution providers that are involved with container stuffing/de-stuffing, LTL, FTL, inventory management and shipping online orders). Dry warehouses are large well-ventilated spaces that can be heated or unheated and provide ample space for large, racked inventory storage or space for machines to process and move materials or merchandise around.
General warehouses may be a single or multi-story and can include office and retail spaces. Special building attention needs to be paid for any location that’s involved with storing or using chemicals and petroleum products or in the lucrative market of data storage.
2. Refrigerated and specialized warehousing
The second general classification for warehousing application is refrigerated units for storing or processing perishable foods and growing crops (as with cannabis cultivation or vertical agriculture). Handling frozen and refrigerated food or pharmaceutical products can be among the most challenging aspect for manufacturers and logistics companies. Food safety, through hygiene and pest control engineering, is an especially primary concern that requires optimum management during transportation and storage. These warehouses are built with specialized insulation and environmental controls to offer a wide range of temperatures for handling food products, including fish, meat, poultry, dairy, fruits and vegetables and confectionary.
North America is the global leader in the global refrigerated warehousing market terms of value and is expected to maintain its dominance. Construction for food warehousing needs to consider allowances for vapor compression, evaporative cooling and blast freezing for food, beverages and healthcare and pharmaceutical products.
Critical considerations for building your ideal warehouse
Several factors are critical to a successful warehousing operation. First of foremost is access and location. It should be no surprise that most warehouses are located along major highlights or transportation arteries or near seaports or airports. Swift and easy access to key border crossings, international airports, are key locations to accessing local markets and North American consumers.
Being in proximity to key customs centres can help reduce complexity and cost, leverage international trade agreements, manage growth and improve customer experience. Of course, not all companies can choose where their business operates. Fortunately, buildings can be built quickly regardless of site to handle all necessary production and storage needs. Every medium- to large-scaled business is going to face issues of storage space and how to expand their operations effectively and affordably.
Construction budget will always be a prime consideration. Building with pre-engineered steel buildings allows you to custom-design your final structure to your exact size and need at an affordable price without compromising strength and features. Warehousing buildings are more than a simple square shell – special features are added to address operational needs.
Important factors include easy access for loading and unloading with large bays and doors for transports to easily locate and park next to, secured 24-hour access (for the staff you want in), pest controls and sanitation systems to meet health requirements. Warehouse automation and electronic inventory data systems and are innovations that can be incorporated into a new build. A wide variety of control systems can also be built into the structure: security (alarms, security systems, CCTV cameras – all monitored as part of a robust security system), temperature controls, electrical and environmental systems, technology for product handling equipment. No sound warehouse is complete without a full sprinkler system, proper drainage and humidity controls, especially for food service operations.
Build the ideal warehouse by planning for future needs
An investment into more working space gives you effective return-on-investment and increased revenues for decades to come. Summit Steel Buildings provides custom pre-engineered steel warehousing solutions that can be built quickly and cost effectively to meet the demands of your specific industry. We will provide you with an ideal dry or refrigerated warehouse as your one turnkey building supplier. Contact us for a free quote.
About the author
Frank Melo has a construction civil engineering technology and business background with over 25 years of experience as a business owner and contractor. He was born and educated in London, Ontario and now divides his time between projects primarily in Ontario and British Columbia. He can be contacted at Summit Steel Buildings at (778) 951-4766 or by email at frank.melo@summitsteelbuildings.com or through LinkedIn.