The danger of production bottlenecks has a simple solution
A case study from The Profit’s “Raise the Roof” episode demonstrates the value that’s created from expanding production through an addition of a steel building.
Kicking up tiny dust clouds from newly hewn sawdust with each step, Marcus Lemonis is exploring a busy industrial operation outside Cedar City, Utah with Jamie and Chris Jaussi, the owners of Zip Kit Homes. The celebrity business investor of CNBC’s The Profit is curious and excited as the owners proudly guide him on a tour of their production area.
The brightly lit building echoes with the screeching sound of saws and jovial conversation of workers. Crews are busy cutting and assembling individual components that make up new prefabricated kit houses, which will be later transported to their permanent location. The working is space is organized, with raw materials in neat, numbered piles so crews don’t have to move far to grab the next piece. The spacious brown and white pre-engineered building serves as their manufacturing facility for each of the two kit homes they build each week. Lemonis warmly greets the employees and learns what each person does to contribute to the end product. He’s looking to understand each step of their manufacturing process to ultimately see if any opportunities for efficiency exist and how he can help the business scale up.
It doesn’t take Lemonis long to realize that production is being bottlenecked by only having one assembly area. He immediately suggests building an extension or a complementary new steel structure that would more than double the number of homes the company can produce each week. He explains the resulting increase in production can contribute even more to the volume of their annual revenue. Later in the show, viewers get to see the stylish new addition that solves the issue that was stagnating company growth and preventing the business from reaching its full potential.
The expansion of Zip Kit Homes’ company’s footprint by adding a second steel building was the exact solution they needed. The new structure created enough room to add the required second production/assembly area and better organize their production flow and storage space. The cost was minimal yet helped increase both their speed of completion and the number of units to be produced in a year by two-and-a-half times.
Many companies face similar growth challenges, whether they’re a young company or well established. In most cases, the lesson to learn is that a small investment in operations capacity can result in a dramatic improvement in profitability. Investing in the right areas to improve capacity management creates immense efficiencies. Just imagine what a similar investment to your production space can do for your bottom line.
The danger of operation bottlenecks
Capacity management is the process that allows businesses to maximize their potential activities and production output. It determines how much companies can achieve or produce within a given period. Capacity management also requires calculating the proportion of space being allocated to production – too much unused space is bad (excess rent, insurance and utility costs for empty spaces), as is not having enough space to allow crews to work to their maximum potential.
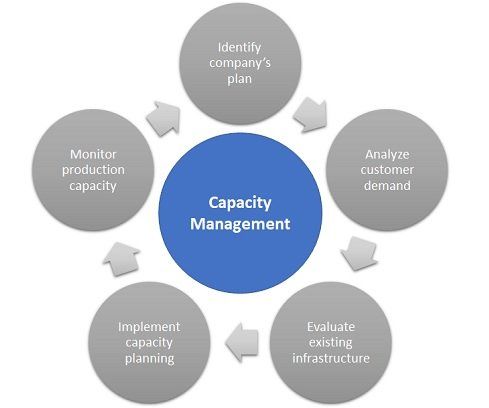
Most of the principles may be well-understood by experienced operations managers. But bottlenecks exist in every operation. Even the people doing the work may not realize the potential that can come if more units were available to be produced and sold. As demonstrated by Zip Kit Homes’ situation, management and production crews can get caught up in trying to fill orders based on their existing circumstances, not seeing the potential growth opportunities around them. As organized as they may be, the ability to increase production sometimes only needs a quick investment in more working space.
Be sure to organize equipment layout first as it will contribute to return-on-investment (ROI) by avoiding assembly line and production flow bottlenecks as much as possible. Adequate production and assembly room keeps operations organized and nimble. Greater space can make operations more cost-efficient and prevent diminished revenues from unfilled orders, delays, customer attrition and decreased market share.
More space = more production = more revenue = more profit
Gains in production volume increase revenues, not just once, but for the lifetime of your business. The investment in a new metal structure may run in the thousands but can lead to permanent increases in revenue and profits in the millions.
A reasonable, cost-effective investment provides greater workplace efficiency. More workspace leads to increased safety levels, happier employees and keeps production areas and inventory more organized and protected.
Pre-engineered steel buildings are not only an affordable investment into your business, they can also be built quickly around existing facilities, equipment and infrastructure. With minimal interruption to existing production activity, your business operates as usual until the new facility is ready for use. Once completed, your teams will be able to work easier, faster and increased productivity – all factors that will drive business success for years to come.
Summit Steel Buildings has worked with many companies to build expansion structures simultaneously to running operations. For instance, Alta Forest Products’ plant in Morton, Washington was designed and erected in between existing buildings using engineering to cantilever over an existing building with columns piercing through roof system and placed to avoid existing equipment. It features a partial mezzanine system to support mechanical equipment and was engineered for a five-ton crane system.
When you’re ready to expand, we're ready to build
Marcus Lemonis was able to help Zip Kit Homes by offering a production solution that was a simple, fast and cost-effective investment into their future success. Lemonis’ capacity management observations led to a key insight: Expand the building space, increase production, triple revenue and profits. Adding additional steel buildings is not only a smart investment, it’s a sustainable driver of growth that will continue to benefit your company’s bottom line, its share price and even shareholder value. All these gains can have an immeasurable increase in the perception and financial presence of your company on a world stage. Get started by optimizing your production capacity to its fullest and meet current and future customer demand with all the resources at your disposal.
We’d love to work with you on your next construction project.
Visit our Contact page and Summit Steel Buildings will provide you with a free consultation and quote.
About the author
Darren Sperling has specialized in the engineering and delivery of pre-engineered steel buildings for over 15 years and has experience in over 20 countries worldwide. He can be contacted at Summit Steel Buildings at (877) 417-8335, by email at darren.sperling@summitsteelbuildings.com or on LinkedIn.